Blog Credit: Abby Jenkins, March 7, 2022 (What Is an Inventory Item? | NetSuite)
Some businesses make things, some sell things, and some do both. Each of those “things” becomes an inventory item for a company, and all of them together constitute a company’s inventory — usually physical assets from which the business generates revenue. Like all valuable business assets, inventory must be tracked and proactively managed for a business to be successful. So “inventory item” has a dual meaning: It can mean the asset itself or the asset’s entry in an inventory management system. Inventory items are the basic building blocks of every inventory management system, whether it’s a paper-and-pencil system or a sophisticated enterprise resource planning (ERP) system.
Achieve Better Business Results with NetSuite & Circular Edge
Grow and scale your business while gaining a competitive advantage with NetSuite’s best-in-class integrated cloud business software and Circular Edge’s expertise in NetSuite implementation, advisory, managed services and direct staffing. Let us show you how to leverage our direct staff pool of resources to realize better insights, organizational efficiency, increased profitability and improved relationships with your suppliers and customers – and ultimately take your business to the next level.
Contact Circular Edge today to learn more about our NetSuite consulting services.
"*" indicates required fields
What Is an Inventory Item?
In simple terms, an inventory item represents the goods a company has for sale or the materials needed to create those goods. An item’s stage of production will determine which inventory category it is counted in: raw materials, works-in-progress or finished goods — this is sellable inventory that this article will refer to. Inventory can also be maintenance, repair, and operation (MRO) inventory, non-sellable inventory needed for manufacturing that isn’t a part of finished goods.
Inventory items usually are physical assets companies can measure and count. For example, a bakery would list all the ingredients needed to prepare its treats — like flour, sugar, yeast, salt and milk — as inventory items. Baking pans and ovens are not inventory; they’re capital equipment. Certain industries may consider intangible items as part of their inventory. In travel and hospitality, for example, hotels consider available room nights as inventory, and airlines’ inventory include seats on flights.
In an inventory management system, inventory items are database entries that contain all the data fields needed to fully describe the item, along with many potential related fields. For example, in addition to information about the cost to manufacture an item and what countries the item’s components were sourced from (which is important for compliance with international trade regulations and for calculating tariffs), the entry of an item meant for retail sale would also include a stocking unit (SKU) number and another for shipping parameters.
Types of Sellable Inventory Items
- Raw materials or components are the ingredients needed to manufacture goods for a company to sell, and they typically can’t be recognized once they’re turned into finished goods. To carry forward the bakery example, before all of its delicious-looking treats appear on the shelf, they have to be “manufactured.” So, the eggs, sugar, flour, milk, sprinkles and chocolate are the raw materials. Not all industries need or use raw materials; they’re mostly inventory for the manufacturing industry. Components are like raw materials, except they can still be recognized once part of a finished good — things like bolts, screws, handles, etc.
- Work-in-progress refers to items that are at some stage in the manufacturing and packaging process but not yet set for distribution or sale. It can include items awaiting packaging or quality control checks as well as packaged items. At the bakery, work-in-progress items could include trays of cookies waiting to be boxed, loaves of bread on cooling racks or cakes out of the oven but not yet frosted.
- Finished goods are those that have passed through all the production points and are ready to hit the marketplace for sale. Essentially, finished goods are the merchandise you might see on store shelves. The bakery’s finished goods are the boxes of cookies, the sliced and bagged loaves of bread and the fully decorated cake.
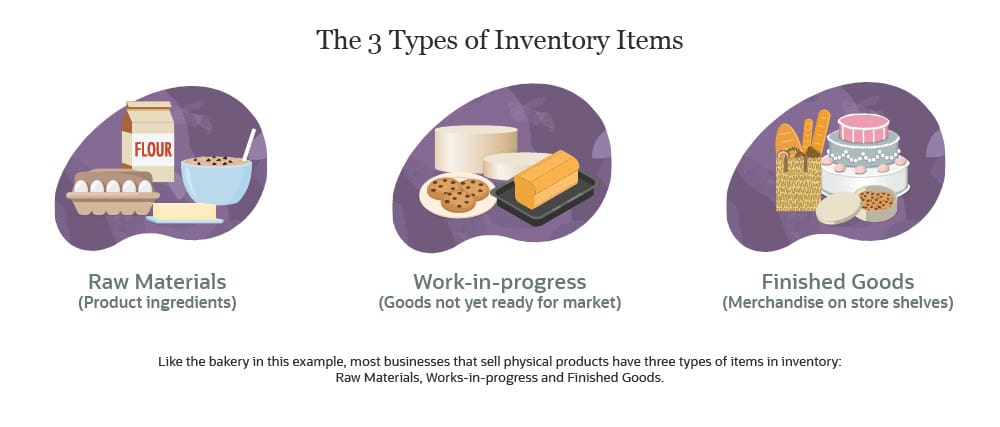
Some businesses, however, have more complex operations than a bakery. These businesses may maintain other types of inventory items, such as:
- MRO inventory. Maintenance, repair and operating supplies are integral in daily operations, particularly in manufacturing industries. These items keep the machines and other production-line equipment functioning. Examples of MRO inventory include screws, nuts and bolts, machine lubricants, coolants and uniforms.
- Buffer inventory. Also referred to as “safety stock,” these items are kept in storage to prevent out-of-stock situations when market movements can’t always be forecasted. Think of a supermarket ahead of a big storm. If it has enough buffer inventory, then everyone can buy milk, bread and paper towels. If not, some people will be disappointed.
- Cycle inventory. These items are ordered in large amounts on a regular basis. Using the baked goods company example, ingredients such as flour, milk, eggs and cupcake wrappers could be considered cycle inventory.
- Decoupling inventory. Much manufacturing work gets done by multiple machines, with Machine A feeding into Machine B into Machine C. If using decoupling inventory, a manufacturer may put some work-in-progress items from Machine B aside, just in case that machine were to break down or otherwise not produce its typical amount. That way, the company can use the stored work-in-progress inventory made earlier by Machine B to feed Machine C in the event of an unanticipated low-stock situation.
- Transit inventory. Items being moved from one place to another are called transit inventory. They could include any of the three basic categories of inventory items.
- Service inventory. How much service a business can offer in a certain time frame is referred to as service inventory. For example, a boutique hotel with 44 rooms has a service inventory of 308 one-night stays per week.
- Excess inventory. This is unsold or unused raw materials. A company must account for any expenses tied to storing this stock that it may not use or sell.
How to Describe Inventory Items
Keeping stock of the stock requires an effective and efficient inventory list, typically generated by the descriptions entered on each inventory item. Inputting those descriptions in a smart way helps streamline subsequent management decision-making.
- Begin with a noun. Adjectives are important — but never as the first words of an inventory item description. Why? Because a store or warehouse might have 500 “large” items or 500 “green” items, so if those are the first two words in an item’s description, a business manager could waste time scrolling up and down a long list looking for that “large green salad dish.” Descriptions should begin with a generic name of the item, like “Dish,” followed by descriptive adjectives, like “porcelain, green, large.” Another example: “Wheel, Mustang, magnesium, 15 X 7, 1965-1973.”
- Avoid information overload. Use only the descriptors necessary to define the item uniquely on the list. Stick to things such as type of item, color and size. Other item codes, such as country of origin or expiration dates, don’t need to be in the inventory item description. Different inventory item fields exist to include these types of details.
- Be functional, not conversational. The most important rule of thumb for describing inventory items is not to describe them the way you would speak about or refer to them in conversation. Instead, write functional descriptions about items to optimize their later use by the business’s managers and other professionals. Remember, it’s about effective use of the inventory list.
- Align with the business. Inventory lists should uncomplicate business life, making it more efficient. It’s important to think through the optimal way in which inventory item reports could be used by the business and then include in the description all the data fields necessary to streamline those processes. Besides a unique name and description, an inventory for a chain of retail stores, for example, should include a SKU number, single-unit price, volume-discounted prices (if any), quantity in local stock, other stores/warehouses, reorder point and estimated reorder delivery times — all information that a retailer on the sales floor may need at a moment’s notice.
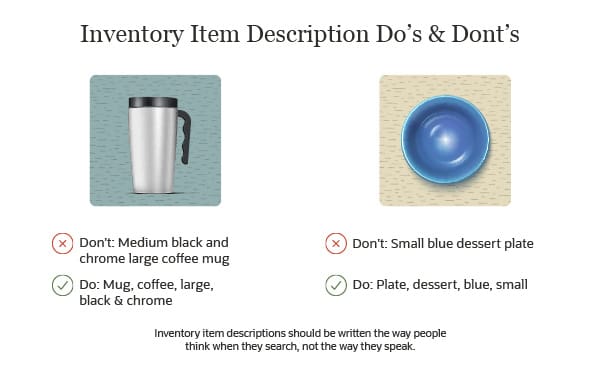
Manage Inventory Items With Software
Managing inventory properly is integral to the success of a product-oriented business. At any point in time, businesses must determine exactly what they have in stock, where it is located, when to order more and how to balance supply and demand based on seasonality and forecasting. Good inventory management software helps companies accomplish these goals. Businesses that deploy NetSuite Inventory Management, for example, can view their inventory in real time across all locations and sales channels. Demand-based planning leverages the business’s historical data to help optimize inventory levels throughout the year, reduce costs from overbuying and minimize out-of-stock moments. NetSuite’s tools can automate inventory tracking, dynamically manage reordering, trace an item after ordering and generate tasks and alerts for designated business team members.
Conclusion
The more inventory a modern business has, the more important it becomes to manage that inventory well. Strong inventory practices begin with inventory item descriptions — the foundation on which the entire inventory management system depends. Best practices for individual inventory item descriptions make for a more effective inventory list for employees and a more effective inventory management system overall. Managing inventory properly from the ground up helps the process run smoother.
Inventory Item FAQs
What is an example of inventory?
Inventory is the items/merchandise a company has to sell, as well as the materials needed to create those products. The three main categories of inventory are raw materials, work-in-progress and finished goods. An example of raw materials inventory would be the magnesium in an alloy wheel. An unpolished wheel would be placed in work-in-progress inventory, and the polished wheel is placed in finished goods inventory.
How do you list items in inventory?
When creating inventory items, keep their descriptions unique and simple. Always start with what it is first (the noun), followed by what it looks like (the adjectives). This way, it makes locating items on the list quicker and easier. Avoid cramming too much information into the item description itself; let the other data fields provide needed additional information.
What is considered a non-inventory item?
Non-inventory items may be physical products a company purchases and then quickly resells to customers or intangible items for sale like a conference fee. What non-inventory items all have in common is that the business does not track them, for a variety of different reasons. They can include items bought for company use, like office supplies, or goods bought for a specific project and then quickly invoiced or sold to the customer. A custom-made sink for a kitchen installation is an example of an item purchased by a company and resold to the customer.
What is an inventory list?
An inventory list is a complete and itemized record of everything a company has in stock, be it for sale, for use or both. It can include raw materials, work-in-progress items and finished goods. Such a list helps to understand item availability and what the business is selling and has available to sell.